Grain Ramblings
I think grain is a deceptive substance, unpredictable and predictable in both its unpredictability and its predictability. When you least expect it, it nose dives, in a split cut, half the tenon or dovetail disappears. When the grain circumnavigates a knot and we think it will never plane on one side or the other of it the grain comes out smoother than silk. Of course, the exact opposite happens too. If we look at wood as a rectangular block, with surface-treated faces made level, straight and square, or shaped and left smooth, and with or without texture, without considering its inner workings of cells and fibres, strands and a mass of chemistry, we might as well think of it more as a section of plastic or other material and even an engineered material such as fibreboard which is also made up of mixed materials a large percentage of which is pulverised wood.
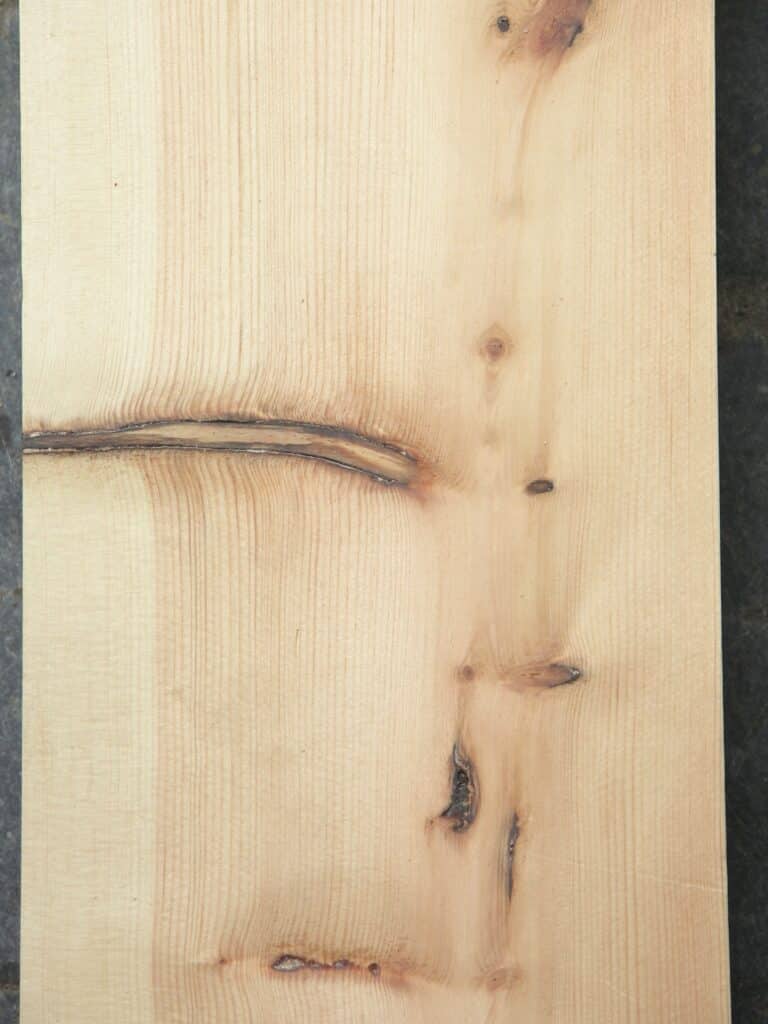
Unlike other materials created to emulate wood, wood is a hygroscopic material that takes up and releases moisture in accordance with the surrounding moisture levels suspended in the atmosphere. High levels of water, humidity, is readily absorbed into wood, and when this happens the wood expands in its width and thickness. Conversely, low levels of atmospheric moisture will lower the level of moisture held in the wood fibres. With absorption and release comes expansion in the width and thickness of wood, or shrinkage, all according to moisture content. And here comes yet another sphere of unpredictability. In the evening you left your newly planed and trued wood on the bench dead flat and the following morning it looked more like a banana. Waah!

I’m sitting in a cafe where I mostly write and all of the tables are dead flat. Running my fingers over the tabletops, they are smooth and feel fine. The tables, about fifty of them, are made from solid oak and I think that they look nice but would be better unstained. Considering the abuse cafe tables get from spillage, these tables hold up. Not one of them shows any sign of a cracking or separation in the narrow laminations and this is the reason they go for narrow laminations rather than wide boards. For mass-making, laminating tabletops ensures that the tables will stay flat, but more than that, any attempt at rebellion from one piece is countered by the dominance of the masses either side. Laminating this way holds and constrains any proclivity to distort through the absorption and release of moisture in the wood. Of course, a waterborne, water-based finish as a surface treatment basically shrinkwraps the wood throughout with its plastic-based resin coat. Cafe tables of this type are always finished as well on the underside of the table as the table’s topside. The corners are never sharp and always rounded. This is no different when using paint. Why? Varnishes and paints stretch in their shrinkability. This seems a false dichotomy. Does it stretch or does it shrink? Can it do both?

Applying most wood finishes, whether clear or pigmented, begins by placing the material on the surface via paintbrush, paint roller or spray. I say place because that’s what painting and varnishing does. The layers are built up and in almost all cases adhere to one another. The exception is shellac, which capably dissolves the first coat into the second and subsequent coats resulting in a single coat applied several times. These finishes dry and the surface becomes taut through shrinkage. If the corners are sharp-edged and 90-degrees one to the other the applied finish becomes super thin at that point and breaks or parts off into discontinuity between any adjacent surfaces along these corners. Rounding the corners even minimally allows the finish to wrap around the corner as a continuous unbroken film.
Many woods benefit from the different ways the boards are slabbed from the tree stem (trunk). Quartersaw wood offers greater stability because the resultant wood is best able to accept increases and decreases of moisture in equal measure from both sides or faces of the wood; this has much to do with wood density (specific gravity) levels, period and division of annular growth (earlywood and latewood porosity) and the arrangements or grain presentation of cells. The resistance in certain cut types as in plainsawn can and often differs due to the obliqueness of the growth rings, etc, and the uptake of moisture content be that via direct water or water vapour as in relative humidity, etc.

On the oak cafe tables, I noticed how the plainsawn wood seemed to remain smoother and more even than on the quartersawn which had the hint of a washboard effect.

Of course, oak being coarse-grained and of more variable density surrounding the growth rings, the surface texturing tends to be more diverse and exaggerated. Other hardwoods such as beech, ash walnut and so on give a consistent surface smoothness.
I have been woodworking for years. But most of my work is done with power tools vs hand tools. Your work is gorgeous and leaves me in awe. It makes me want to dip a toe into traditional woodworking ie; hand planes vs power planer. What are some of the basic hand planes someone should have?
Hello Michael, I highly recommend to you to visit commonwoodworking.com to see the basic tools you’ll need.
Grain is at once the fascination, frustration, and challenge for woodworkers. Thanks for the great post.
Paul, this was a very cool post. Especially liked the way you pointed out slight “ridging” on the quarter sawn oak compared to the flat sawn stuff. 1/1000 inch!
Paul, you need a proof reader. There are several places where commas are needed to punctuate properly. The second sentence doesn’t make sense. In the fourth sentence, the word “would” should be “wood”. Are you using a voice to text app?
Dear Kevin,
whilst most probably technically right, the prose and verse of Paul’s texts comes through proud, honest and elucidating to me. I prefer clear text with some typographical warts to grammatically immaculate nonsense any day, and immensely enjoyed reading about wood grains presented more succinctly here than any of my meagre reference literature.
Last sentence:
.. than IN any of my …
I’m not a purist. I enjoy this blog. I just found this post difficult to read. Several times I had to reread a sentence more than once to have it make sense.
I had written and did not go back through as I usually do, several times, or perhaps I thought I did. Thanks for the nudge though. I know it is annoying reading anything that’s missing that comma that makes sense of what otherwise becomes nonsensical. Rereading it it did have a few sentences that made no sense even to me. I think I fixed most of it now.
As to your suggestion of having my writing proofread. This would really hinder the whole of my intent in presenting what I do. Anything between writing and hitting publish is just another step. Your very legitimate complaint is perhaps one of three I might get in a given year and though I realise that most people just tolerate my less than perfect grammar, I think they get what’s written and the reasons for it. I think you might rethink the suggestion of a proofreader in light of the reality that I have written and posted 3,000 of these blog posts on this site alone and who I would get to proofread such an amount of work I do not know. Certainly, I could not afford such added cost to what is always free. Anyway, thanks for putting up with me. I will do as I did in school when they told my parents (and me) that I could never be educated and try harder.
Great article Paul. Grain is fascinating. Trees are, to me, like people.
Everyone is different yet we’re all of the same human species. And then the grain is like our personality’s & physical characteristics so different from one to the next.
I enjoy the technical aspects or abstract I should say that you delve deep into when you write articles. I seem to not have a deciphering any spelling/grammar mistakes. No biggie.
All the best Paul
Thanks for making it all happen Paul … and mistakes of grammar, punctuation are welcome in my world. As you note, the spontaneity of a post is often one of its great values.
The obvious immediacy of your posts are a value in themselves as they bring along with them that sense of wonder and emotion that draws me to working with wood.
I’ll gladly trade the ability to read a post firmly embedded in the “now” of introspection for the often colder, post-proofreader style of writing.
Remember, also, Kevin, as I think it was George Bernard Shaw once said, “The English and Americans are separated by a common language!”
Regards,
A “Bloody Colonial”
Kevin, Paul is a poet and doesnt now it!
Every college paper I wrote was pure poetry (to me).
Thanks!
It got me too, as I was concluding in my reply😂……
Should have read, ” I seem to be able to decipher any spelling/grammar mistakes and get the gist of what your saying. No biggie, to me. I seem to not have a deciphering any spelling/grammar mistakes. No biggie, to me.
😂🤦🏻♂️🤷🏻♂️
Paul, what happens when we rive a board in respect to the grain surface? I know the basic cuts in oak well by now – flat, rift and quarter. I know how the surface of boards with those properties will behave and look in oak – but since I have made lumber out of a big oak tree, I know that my square (at least they were…) planks are cut from a tree trunk that is conical. Would it be better to rive planks than to cut them? Would it give me better furniture materials than quarter- or rift sawn wood? And if so, what would you consider to be the benefits?
I do have some very straight-grained pieces lying about for riving dowel blanks, so I do get the benefit in those kind of applications. But for, say, a table top?
Mind you, I am not considering the labor involved nor the yield – I am after material quality here. Transforming a 20 metre tree into mostly quartersawn planks was quite an ordeal in and of itself – but as a hobbyist I can indulge in the more labor intensive ways if I want to.
Hi Paul.
I was taught to take the arris of the edges of with Sandpaper just enough especially for paint to key to it other wise it is one area that paint starts to break down. All so it feels better than a sharp arris.
Rounding is superior to an arris removal as the now two-cornered corner of the quarter-octagon created by the arris is still sharper than a gentle round-over, which is as I said continuous.
Good post Paul.
Very interesting.
The negative criticism rubs me againt the grain though.
I don’t normally make the effort to comment on these posts but with this one, how could I not? 😉 Thanks Paul.
I’m an ex engineer and architectural metalworker, now working in a high school in London as a workshop technician. I also run a very successful part time carpentry business. All good woodworkers (women and men) learn very quickly that wood is a natural organic product, and although beautiful, has many faults: it warps, splits, cracks, has wild grain that tears, and has a knot just where you want that dovetail joint. A good crafts person learns to control and connect with the material they’re using, to the best advantage. That’s what being a crafts person is all about: controlling the tools AND the materials.
I know that this is not really wholly true and then true too, Kevin. I will say this: I don’t know of any time where wood has been selected that the maker will not have considered wood with a knot where a dovetail joint will be made, be that pins or tails. In my fifty-seven years, I never have. Most wood doesn’t crack after it has been selected, prepared and acclimated with care for the piece and then the joinery, and it usually doesn’t warp at that stage either unless it is indeed still with high moisture levels in it and it’s going to somewhere with lower levels.