Where Freedom Thrives Most . . .
. . . is in the lives of its maker hosts!
Things changed with COVID. Life. No masks now, freedoms back, but something did shift in every culture like a swelling sea that never settled back to the same levels past. We lived through extreme extremes of different kinds with effects that affected all people differently. Some of us got COVID with dire consequences while some just skated through it with nothing more than its distraction. Ukrania stands between Russian aggression and the rest of the so-called free world and the extremes as with any war are felt on a global scale. We cannot ignore such impacts in physical or spiritual realms. We can only take control as much as possible within the sphere of our own limitations. Within my own sphere, I am glad that we have ably continued our outreach quest to reach and teach real woodworking. Here, we work soberly and solidly to bring sanity beyond the insaneness of brutality by simply training woodworkers everywhere we can. Our expansion continues, albeit slowly and perhaps a little less interestingly without the razmataz, but it’s less about numbers than it is about truth. Often, as happened this morning even, someone will say something like, “I cheated and used my tablesaw. . . ” to do this or that “. . . because it was quicker and easier.”, not realising it wasn’t quicker nor easier, it was that he always chose what he saw as the easy route because he never developed real skillfulness with hand work. My week, as yours, has just begun. I have wood stood by the end of my workbench acclimating together with plans roughed out for the bed I started making this week. Oak’s own characteristic aroma is given off with each cut I make and the shop fills with a scent that ebbs and flows in the atmospheric swelling. When I arrived yesterday the scent wasn’t so powerful as when moisture is given off, but cutting into it was just enough to translate me back to the days when such kiln-dried wood became a thousand walking canes and by the end of the month UPS picked up my boxes from the workshop to deliver them all over the USA.

Designing and making are two equal parts — two halves of the same coin — and, though opposite sides, they interplay conspicuously throughout a given day of flipping to make. Though common enough for me as a designer and maker, I see it as no ordinary thing. Hyphenating designer and maker doesn’t make it a single entity but two distinct elements of a maker-designer’s life. Scraps of paper often carry the lines of an idea be that by drawings, sketches or words, through these things something emerges as if from nowhere to encapsulate the ideas more solidly. The overall concept always comes together just fine but then the joints need formulating and decisions of engineering must be thought through and considered more deeply long before you get too much made.
Hannah comes in in the midst of things, always pops her head around the door, says, “Hi, Paul!” and skirts through to her bench where her tools and wood wait and in minutes she’s making. She’s self-motivated and direct. You sense her excitedness through her movements even if she’s in a different space and I only hear it as she lifts each tool to work. This lived inspiration is more viscerally discerned in the presence of some people. John is just the same. Inspiration never grows old, never tires, is never outdated and the logs in the fire of creativity spark off the creatives to ignite one another throughout the day.

Hannah’s been busy these past weeks making small things to sell at craft venues and has done well. Selling things you made from scraps and boards rough-sawn translates into income, yes, but more than that, for young makers it validates you as creative enough and sufficiently skilled to make your living from it. What’s all the more valuable is that this was all made by hand and not machine. What’s the difference? Well, if you have to ask there is no point my really explaining. There was amazing skill and dexterity in what she did. Use your imagination. It’s rough-sawn, unsquare, unstraight and she sharpens a plane and saw as needed to make the wood work for her. I know I am preaching to the choir here on my blog but there’s a message in it. She’s skilled in all spheres hand made and she’s selling her work.

Six years or so ago, when Hannah came and had never used a plane and never experienced sharp chisels, she was a maker yet to emerge. She’d never made a dovetail or a mortise and tenon and then, just two years later, she’d made her toolbox at top. All that she had gone through up until then was the foundational woodworking course I put together for people starting out that I still use in all my training and teaching here online and elsewhere She’d made her bench from studs and taken it home to continue working there.

Three years ago Hannah and I found ourselves involved in transferring our skills and knowledge to support workers at a centre for young autistics learning to cope with the adult world. Up until our arrival, machines and a machinist were taking centre stage in teaching and training young autist adult woodworking. This seemed very incongruous to me. The exact opposite to what was needed. It was at this point that Hannah took on the mantle of teacher and she and I began training the support workers to work with hand tools and support their autists in the craft workshops and through them, we reached into lives we might never have reached at the centre. Hannah had a remarkable ability to communicate her skills in a highly relatable way, often without words, and suddenly I saw her as both a skilled maker and teacher. These are the remarkable things that just leave you dumbstruck, asking yourself, “Now where did this come from?”

John has been teaching and making and he too enlivens the shop through interactions of different kinds. In his making, he makes beautiful cajones. These are not the mass-made versions but the hand-made, hand-planed opposites with all the internal surfaces hand-planed and scraped to maximise the crispness of the internal surfaces to give projection and crystalise clarity. These are the ones you can’t buy because hand-makers like John rely on planed and not abraded surfaces that tend to dull and muffle the sound. Of course, the interlocking dovetails, all hand cut, 40 of them, exemplify the signature of a master in his craft, but then there are the hidden details you will never see and know of. Makers use thin, three- or five-ply plywood for the tap and percussion panel for strength, but the solid wood panel facing it has an unusual joint around the rim of the Cajon that fits tightly into its groove all around. This allows for any shrinkage that might take place. Without this unique feature, the panel will often split irreparably.

John too is a remarkable maker-cum-teacher. He works with Jack to teach and train alongside me each week but now has begun his own one-day beginner classes here at the workshop. Hard to imagine our first encounter back in 2007 when he came to my home garage to make a workbench as a first project. I had taken a sabbatical from my US work for a year back then and came back to the UK which was good. We’ve been friends ever since and we bounce ideas off one another constantly in the day-to-day. “Hey, John! Have you ever tried this?”
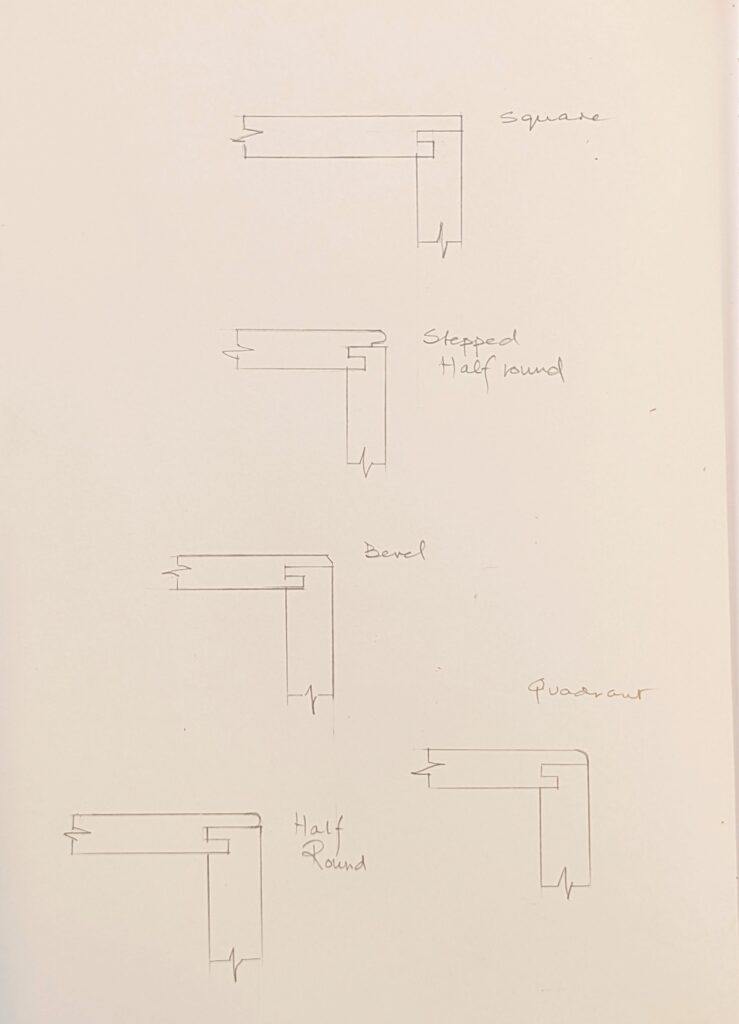
The beat panel made of thin plywood is simply screwed as a very basic panel in place to the sides top and bottom, but the front panel with the hole is let into grooves around the rim. This was a suggestion I made to John as he was building and I suggested it because it was a joint I used when I designed the two credenzas for the White House on some panels I wanted from solid wood. On these pieces, we allowed no engineered boards as is the modern trend for furniture pieces with veneered facades on MDF. Above are some options for the panel corners. There are several more and it is a matter of personal choice. This neat-looking joint always looks good even if shrinkage does take place but if you dry the panel down enough you should have no shrinkage issues occurring anywhere.

Yesterday I began dimensioning my oak for the new bed. It’s often assumed that I either buy in my wood ready planed and milled to size or own machines to do that with. I don’t. I have no real need for them, though I admit they are much easier when it comes to dimensioning wood. Beyond that though, what about you? Would I be cheating you of realness — the genuine article, were I to mill all of my stock using machines only and telling you to do it by hand? Of course, I would.
Though I value the hand work mainly for the intrinsic value sentiency brings to my life, I really value the use of it for the higher demand it requires of me in connecting to my work, the wood, the environment I work in and then too the interplay all of the components wrought in realms mostly I see as actually undefined. I think we underestimate the importance of exercise for our physical and mental well-being through interactions handwork demands of us — something never even approached by machining simply because machines are designed to minimise the need for human input, physical endurance and skill, especially skill. What’s the saying? “Use it or lose it!” and, “No pain, no gain!”

I understand that the manual-type work of which I speak can be painful for those with diseases, diseases such as arthritis, multiple sclerosis and then many other disabilities too, and it is better to use machines if the disease would otherwise stop you from woodworking — no question about that. I think we should consider too, though, that there is the art of living making the unmade into the made that has hidden benefits we might not always recognise. And I mean by hand as a usual course in making. I recall one time needing some coving for a piece I was making and needed to conclude for a birthday gift. In the machine shop, I rigged up the tablesaw with a diagonal fence to run my board against. By raising the blade incrementally, the cove came to be in about fifteen minutes. Once roughed out it needed scraping with a round scraper followed by sanding. When it was shaped and ready for mitring and then fitting, I realised how skilless the whole thing was. An hour later I felt robbed. Up until that hour, the whole piece had been so thoroughly satisfying to make by hand that I actually didn’t really want the work to stop. But I hasten to say here that I never saw it as many people do when they say, “Well, I did cheat a bit for this or that!” when they used some power equipment to cut something like a dovetail. It wasn’t me cheating by using a piece of power equipment. I did cheat though. I cheated myself of the satisfaction I now get all the time, every day in the making of things handmade. Do I cheat by using the bandsaw to rip big cuts? Not a bit of it. Would I cheat if I had weak parts to my body through a disease or an injury? No, no, no!

So just when do we cheat? I am not sure that most woodworkers do. If I were a woodworker and I chose to do most of the work with a machine, many jigs and so-called power tools, there is nothing ‘cheaty‘ about it. If someone ordered a project and said they wanted only handwork and no machines to be used and I did it all or even mostly by machine, I, me, personally, would be cheating them. It is not so easy to define handmade in our day and age as most machine work is for some very strange and mysterious reason referred to as handmade. But if wood is planed and trued by machines like planers, thicknessers and then sanding thicknessers too, and then the remaining work of joinery, fitting, shaping and so on is hand cut and done with hand tools, then I believe it to be hand made even though some machines were used for dimensioning. Somehow, for me, it’s when the hand tools and the hands, the manipulation of the tools as in hand tools and not machines, have the final say, that makes the difference. For myself, I understand how captivating machines can be, especially if you never mastered hand tools. Most hand tool operations can be adapted to machine processing. I once devised a method for routing out bowls to wooden spoons that could be completed identically in every spoon a thousand times in as many minutes. At $18 a pop that would have been good production along with high profitability. After the first few, I ditched two days of development to set up the work and went back to hand-cutting them with a gouge. Why? They were not handmade anymore. I allowed a brief skirmish with an invasion of an enemy to my wellbeing. Going back to sanity, I ended up where I could comfortably carve a bowl of the spoon in about five minutes, depending on the wood. Cherry, maple — easy!

It’s less about cheating others and more about cheating yourself. In business, with competitors, you may have no choice. In high-demand, highly competitive countries and cultures, where life can often indeed be cheapened so, as they are often based solely on economy and commerce, marketing and the industrializing of life, family, education and on into medical care and so on, the choice is mainly taken away from you. This survival of the business-fittest has little to do with holism for individuals to stand alone as individuals fully relating to the greater whole and good of society around them. Competitor supremacy is becoming more the ambition and goal even though it tends to cheapen life alongside its product. As an example, what happened to the Industrial Revolution? It just kept growing and ultimately was exported to the four corners of the world to create a better, more affluent society. From car manufacturing to bikes and bandsaws all made now in Taiwan and then chips (not fish and . . .) in Asia creating what? More good old competition. What value human life, really?
Wow, Paul, I was misdiagnosed throughout childhood, and only found out as an adult that am autistic. I applaud what you’re doing in that realm. Everything about being creative with wood always fascinated me, but a lot of the noise and dust was too much for my senses. Your channel and a hand tool approach has helped me discover a true passion in woodworking.
❤️
It’s puzzling how many people assume that Paul is legalistic and judgmental about what qualifies as real hand work. It’s true that many teachers who strive to meet high standards, and teach others to do the same, become legalistic and judgmental. I appreciate how Paul actively resists that negativity.
Would it be possible in the future of WWMC that John can contribute a cajon building project?
Probably not, Nick. We have no plans to make musical instruments even when they work as furniture pieces. Actually, scale down the side cabinets we just made and some others and you have a Cajon. They are not at all complicated to make really.
Paul, can I ask what wood was used in the Cajon pictured? Or if there are any specific woods I should avoid, or would be better? I’d like to make one for my daughter, but don’t want it to sound bad.
Fantastic post also, the last paragraph especially, very much resonates with me.
I have to ask, was it not possible to make the coves on the clock using a moulding plane by hand as opposed to using the table saw?
I thought I made that clear but perhaps not. It was a one-off that I felt I cheated myself of a more positive outcome and never used that method again. In all of my teaching and making since I have always used hand planes and never would I use a machine of any type again unless I simply couldn’t because of ill health, disability or age. I recall a friend maker who was forced by his boss to use a router and dovetail jig to make a chest of drawers. His work was always exemplary of fine work but he was slow and his boss wanted more speed. The work took half the time, two days instead of four but it showed in two ways. No matter which way you slice it, machined dovetails always look machined and the joints contradicted the whole of the piece which was otherwise singularly made by hand. Secondly, it hurt the maker greatly after decades of always relying on his uncompromised hand working.
I learned very quickly from my mistake. Not in the outcome of what I made, it looked just perfect, but in how it left me afterwards. These are lessons well learned and earned from. I don’t dwell on it bit it is worth pointing out to those with soul!
On Paul’s YouTube video where he makes the “Paul Seller’s clock” he does made some bottom coving by hand.
Off topic, but: I just noticed that the first Masterclasses video, Wallclock Project, was uploaded in mid-October 10 years ago. Did anyone mention or celebrate a _decade_ of Woodworking Masterclasses? Maybe I missed a blog post…
A lot of great bits to take away here, Paul. I am particularly fond of:
“Woodworking is not gender-specific by any kind of intentional exclusion as far as I know.”
I appreciate you mentioning Hannah in some of your posts and acknowledging how unfortunate it is that there is not a more equal balance of genders in this “makersphere”. As one of those female minorities, it’s important to see ourselves represented. While I wouldn’t care either way if I was the only woman doing the work that I do, it does make me feel less alone knowing there are others.
And:
“Would I cheat if I had weak parts to my body through a disease or an injury? No, no, no!”
I have noticed there is a strange aggression from some power-tool woodworkers that push back against hand-tool makers. Some call the practice snobby or elitist but your sentiment is exactly how I feel. If there is no pressure to build a large number of items very quickly or there is no physical limitation, is it really necessary to use power tools? But there are legitimate reasons to use them and it’s not as binary as some people make it out to be.
Thanks for taking the time, Jami. What’s most saddening is that advocacy for woodworking for all hasn’t changed the statistics with regards to women coming seriously to occupy woodworking even though there are some strong women makers as role models. I tried a levelling-up program to dismantle some of the historic biases along with others old and new but still too few takers. Hannah is a perfect example of someone finding her calling successfully. All she needed was a bench, tools and wood.
Indeed. The shyness to woodworking very often starts at the beginning; not being encouraged or supported as a child continues into adulthood. Sometimes people just need access to the tools and a little bit of encouragement and they’re off to the races! Thank you for your advocacy!
I have often thought that we need an actual live and real discussion on this in a much deeper way rather than pussyfooting around semantics, phobia identity and much more. Then we might actually get to the core of what is the problem and what can be done to make the changes happen on acceloration rather than relying on schools that know zero and less about craft and manual working, about as much as academics do, which is nothing in my experience, and get the job done.
I so appreciate you bringing this up Paul, and seeing Hannah’s work through your posts has also been encouraging to me. I am forever grateful to you for making woodworking accessible to the masses, regardless of where they are, how much money they have or how they identify. Thank you.
Scarlett, this triggered a few comments from others who might be well-wishing and well-meaning but just do not get how hard it has been for women to get a good foothold in real working environments. My advice is to stick it out, persevere and set your goals to reengineer your life long-term. Self-employment is your ultimate goal and it may take a few more years to expand your CV and establish yourself. I will gladly help with advice long distance and also if you have tool needs I may have some spare even there in the USA. You are not on your own in this.
Hanna’s apprentice piece is beautiful. My younger sister does some woodworking. She made a baby crib for a friend that later circulated to me when my daughter was born. This gives us another example of how furniture made out of good material with care has a chance to live on and make many people happy. I expect we will see more women woodworking in time, and this will be a good thing! It is too early tell what my own daughter will enjoy, but she does take interest in my workshop and the things I make. We work on little projects together sometimes and she currently hopes to fashion a double wheelchair for two of her dolls that have lost one or both legs. I offered to try to reattach the legs, but she wants a chair for them and it seems an interesting project. We’ve been making sketches and talking about different design options and looking at items we might be able to recycle like some old training wheels from her first bicycle. It is great for kids to have options to make and otherwise explore the world that don’t involve little flat screens!
It is so important what you’re doing here, Mike. It might seem natural to you but encouraging and supporting our daughters to explore skills that have been traditionally reserved for sons is extremely important for her growth. Thank you.
I work in a shared shop-space and for years I have been the only person who isn’t a man. Though I don’t feel unwelcome in the space I find that I consistently am expected to fill a certain gendered role, such as sweeping up the shop/machines, emptying the dust collector and taking out the trash. I am also the only one who cuts joinery by hand and it took a while before the rest of them stopped asking me why I don’t just use a router. There are a lot of dynamics at play that seem obvious to me but perhaps are less so to them, beyond gender there are the privileges of class as well. There is one man who has enough money to buy the latest festool machine whenever he wants, whereas my small collection of hand tools has taken me years to accumulate. I wish these dynamics were discussed more openly. It puts me in a position where I have to speak louder than I care to in order to advocate for myself whereas an open regular discussion might be more productive.
That’s an interesting tale, Scarlett. It seems like you’re laying the groundwork for others to follow, and I’m guessing/hoping that one day soon you won’t be in such a small minority (perhaps majority!). I had enough money to buy Festool kit, which I did. I sold it all again, because it just wasn’t that much fun. A lot of the stuff I had was for renovation work (which I don’t need anymore), but a good portion was my consumerist ego taking over, greatly influenced by youtube! There’s a soullessness to buying the means to the end that I’m still trying to get beyond. You should be proud that you’re already there.
Actually it sounds more like you are being treated as a permanent apprentice. It could well have to do with gender, but it may also be at least in part that you are seen as not “serious” because you use hand tools, or more likely both. If you don’t use the power tools or dust collectors, I would suggest simply leaving the rest of the users/makers to fend for themselves. I’ld seriously think about finding a better environment though. That kind of attitude on the part of the others is immature.
Another here in your comment, John. “I would suggest simply leaving the rest of the users/makers to fend for themselves.” What if she really needs this job? You make seem as though she can indeed just jack it in and walk around the corner and find a, “better environment”. If it is like my 25 years of experience living in the USA and then 38 years here in the UK, most women striving to become woodworkers as a full time job will not be able to just “Leave” the job she has found nor find a “better environment.”
Hi Scarlett, as others have mentioned, if it were me I would clean up the areas I used, and leave the dust collector and powered tool areas to those that use them.
In addition, even with many of the female makers on YouTube, they use machinery (power routers especially) far more than I prefer. Part of that is the monetization of their content. Tool companies often provide them with tools in exchange for featuring those tools in use. So called “loose tenon” joinery has become so popular because of this, with many makers using them on every project even if a true mortice & tenon would be a much better solution. Festool’s Domino has become the defacto joint tool for many, sadly.
Really! Too many assumptions here, I tell you. If Scarlett is working for a company and the company or managers say clean up, sweep up, put away and keep every area clean and clear then she will most likely lose her job if she says I will just do my area and not anyone using power equipment or even more, I’m not doing that. Let’s just get real. What if this is the only step up she might get until she can go it alone or have a good enough CV to find another job? Why on earth would you think she has a choice in this. She might just need the job or the internship, apprenticeship or whatever arrangement she has for a dozen good reasons not the least of which is to earn her living. Too much of, “if it were me I would…” do this and I would do that.
People who did no follow you for long enough should know that the workbench in “Hannah’s corner” is not the workbench she made. She made a very neat workbench (see blog UPDATE ON HANNAH’S PROGRESS dated 19 August 2017).
(I have to say her workbench looks better than mine).
This (perfectly functional) blackened workbench was used in a woodworking seminar in Oxford (2016 or 2017). I have always wandered if you did give it this appearance (black with the rough sawn apron) to stress the fact that a workbench doesn’t need to be a fine piece of furniture, and what is important is what one build with it.
I made this bench from secondhand rough-sawn wood and distressed it anywhere in places I thought it would enhance the overall look of a not-so-new-looking bench but still a new one. It was just handy for someone to use and Hannah was the one. She really needs to make another for herself at work because she is left-hand dominant.
Dear Paul Sellers,
would it be possible to show some hints (image or sketches) to show, how Anna made the legs of this table?
https://paulsellers.com/wp-content/uploads/2022/08/PXL_20220824_130338320-scaled.jpg
Thanks,
Zoltan
She used a rebate plane to create the step-down to the corners, glued and taped corner strips in place and veneered each face for the feet and bevelled the under edges to prevent them from breaking if dragged.
I didn’t notice that the miters were interlocking the first time I saw that photo. That’s really cool. Is there a name for that joint? Tenoned miter?
Paul,
When you design what methodology do you use. Is it just sketches or do you use the traditional plan view, front view, right side view technique. If so, is it done with drafting methods using T square, plastic triangles, erasers ;-), etc. or some particular software on a computer?
Richard
I usually run my ideas past Joseph first so a rough sketch on a piece of wood or paper conveys my idea with the immediacy this supports. I then show the idea to the staff who get to give a vote of confidence in it. From then it is different elevations to scale, a perspective sketch to show three sides and enough to take off measurements for a cutting list. These sketches and drawings ultimately go to Joseph who draws everything up in Sketchup. This serves to find flaws and erroneous elements for correction in the final schematic. Ultimately it becomes the PDF for members to download and follow from. Do I use T squares and triangles, erasers etc? Not for every drawing no, but I do use them quite a bit. I can eyeball most lines for squareness etc no [problem. The drawings are always fast. My new bed took mer an hour or so.
hi paul,
could you please consider doing a blog on different techniques you might use for end joining boards? (eg if you didnt have enough long boards to make your bed head, or the side of a drawer or whatever). i am curious how you might do this when needed from a hand tool perspective.
(or do you just never end join wood, because it never gives a good enough joint?)
many thanks paul
I can recall improvising on an odd occasion but have never done it as a matter of course. It’s not something I see as generally needed except in building construction for carving joints along ridge boards and in some post and beam construction. We furniture makers rarely go longer than 6-8 feet in any direction so not a necessary part of our working.
Paul, I was recently end joining some wood for a laundry drying rack/pulley thing that I’ve been working on. I only had 0.8m and 1.4m length boards, and I needed about 2m. I didn’t want to buy more wood, and there wasn’t much else I could think to make out of the two boards I had, so it was probably quite a specific use case. I used Japanese scarf joints (kanawa tsugi) for this, just because it was decorative, and it offers a marginally better alignment in my opinion (stopping any side to side movement). The pieces were only 22x35mm, so the joint was actually very hard to fashion, but it was fairly succesful, with only minor gaps. The result is a solid frame.
If you absolutely need longer lengths and don’t want to buy new, or have particular wood you want to use, then try a few different scarf joints to see how you get on. I found them really enjoyable to make, quite challenging. Probably not something I’d include in a furniture project unless through necessity though!
thanks paul and rico cheers.
I own a 10″ combo planer/thicknesser, but I really do not like to use it. I find that I have to take off a LOT of material before one face is dead flat. If I just hand plane it flat, I can keep more of the thickness. The thicknesser function on the combo machine is then nice to use to get to uniform thickness fast, but if I need to remove a fair bit of material I just use my band saw as a thicknesser. 🙂
I rip ever so slightly oversize and plane down to my lines, and the offcut can be utilized elsewhere.
Machines can be great, but the control I get from hand tools wins every time. And I love the fact that I usually don’t have to make test pieces! Very few jigs, too..
I cheated today. I made my life easier. I pulled out the crosscut saw and broke down two 6 metre lengths of framing timber on the low wall next to my vehicle . It was quicker than running a lead and easier to carry up the side of the narrow path to the rear of the property I am working at. I cheated by having only just sharpened it thus making my effort easier. I cheated by delaying the quite possible inevitable purchase of a battery powered circular saw, I do admit they have come a long way in a short time. I cheated because I had the option to do so. I haven’t cheated myself by developing an ability with hand tools through learning from others.
Thanks Paul.
I’ve tried Sketchup in the past and with its steep learning curve it turns into a project itself. I agree it would be helpful to bring out places where issues are hiding, but just can’t seem to stick with it long enough to make it work for me. There are lots of details in woodworking that make it both rewarding and frustrating at the same time.
-Richard
Mr. Sellers,
Your musings regarding the meagre representation of women in woodworking brought something to mind that I saw in one of my Taunton Press books about a woman who teaches grade school children woodworking. Turns out it’s in chapter 6 of my copy of The Workshop Book, © 1991, with the particulars of her work between pp 144 to 148. It seems she converted an old city bus with adjustable, kid sized workbenches and travels from school to school during the week to teach her students. She says, “I can teach any kid who can talk to me.”. Her name is Sheila Dawson and I like her attitude. Her bailiwick is the San Diego, California area. Sounds to me like it might be something for the female wood workers who follow you might look into to recruit and train the next generations of young girls to follow them. Its a thought.
Paul,
I hope you keep an open mind around politics because conspiracies and court intrigues are nothing new and should raise an eyebrow when they’re censored.
Nobody “skated through it with nothing more than its distraction” because the covid responses created over 300,000,000 new starving to death people and that’s UN numbers.
You might still have a staff and be making money but consider how many businesses went under- over half of them minority owned businesses.
How many others lost their jobs because of covid vaccine mandates that violated the Nuremberg Code- all to find out that the “anti-vaxxers” were correct because vaccine makers and Fauci and Brix now admit the vaccines never prevented transmission.
Multiple studies show the lockdowns had no effect on reducing cases, deaths, or hospitalizations. It was already known they never would, but China did them, so Fauci followed China.
Meanwhile doctors and professors with top credentials from ivy league schools who gave any opinion contrary to the government’s media-assisted narrative were censored and stripped of those top credentials merely for asking very relevant questions.
Freedom isn’t negotiable for many of your readers and if you delve into sources of information beyond those sponsored by corrupt corporations (Pfizer was involved in one of the largest lawsuits ever for fraud) you may see both sides of the story- and the science- instead of just one.
A note on home workshops regarding insurance:
Hopefully this sort of thing is only relevant to Australian makers. In the last year there have been several cases brought to public attention through the media whereby home and contents insurance policies have been considered null and void as a result of people “running a business” from their home address without adjusting their insurance policy (and presumably the premiums) accordingly.
So please, if anyone does sell stuff they make from a home workshop check your policy.
Paul, I love this article. Cheating is a state of mind, and it is also a matter of truth versus lying. I never let my students cheat. They can do things by hand or with machines, but it’s all about intention. They need to do what they set out to do. My classes are sculpture and 3-dimensional design, so we don’t have enough time to perfect skills before they move on. This is a very important point in the world of being an artist just as much as it is in the world of furniture maker. It is an absolute requirement that time is required to become truly proficient in any field of creativity. Students that think they have achieved a sufficient level of professionalism or ownership of the medium after one class are sadly deluding themselves.
Hi Paul
Thank you so much for your inspiration and many skills that you have taught me over six or more years. A thought. Do third world woodworkers only use hand tools?
In 2017 I taught some lads in a small workshop on a slum in Kampala Uganda set up by Kids Club Kampala. I was primarily there to teach technical drawing to teacher and pupils. However I taught them to make one of your three legged stools. I could not see a brace and bit anywhere so when it came to making the holes the teacher handed me a drill driver with an inch flat bit in it to use. Their very hardwood timber did not take kindly to being drilled with a less than sharp flat bit and the drill driver soon started to smell and complain. I asked if they had a brace and set of bits. One of the students scratched around on the floor behind one of the benches in the corner and came up with a bag with the real gear. Holes were drilled successfully and the teacher said that I had taught him new skill. Very surprising I thought. Glad to spread your gospel to the most needy. Much Blessing.
Sadly many charitable institutions exported the concepts of mass-producing equipment into environments that would have best been kept out. I come across all kinds of centres for advancing craft education to so-called third or emerging countries and cultures such as young adult education for special needs where button pushing has become the new craft norm. Little did we realised such mind-numbing and indeed dumbing down could replace skilled craftsmanship.
“I think we underestimate the importance of exercise for our physical and mental well-being through interactions handwork demands of us — something never even approached by machining simply because machines are designed to minimize the need for human input, physical endurance and skill, especially skill. What’s the saying? “Use it or lose it!” and, “No pain, no gain!”
Well said. I have just pushed all my machines (save band saw and drill press) to a corner, covered them with a tarp, rearranged my basement shop into a hand tool space, and begun a few projects. After 40+ years of “American style woodworking”, at 62, I am starting over. The aches and pains are worth it. I can actually hear the radio now. The space (and the air) is no longer filled with sawdust. The environment is pleasant and I am learning a lot. Thanks to you and the others that continue to serve as guides.
Get ready for fewer aches and pains then Doug. Let the physical therapy begin with some mild (work) bench presses.
Paul would it be cheating if i did most of my work by hand. But used a jointer planer to surface and flattening boards. I do this as i rather cut joints and do fine assembly by hand but using the machine helps speed the project up so i can keep up with lead times. I only do this so i can focus more time on the fine woodworking and not the dull monotonous work that takes so much time by hand to flatten boards although i love to do it. It also helps me save energy for the dovetails and drawer making vs getting boards ready. is that cheating. Thanks John
I don’t really think so, John. Mostly it’s about finding the right balance to fit, match and suit your personal needs and preferences. My main objection, if it is an objection at all, comes from those who think they made a good dovetail joint if and when they used a power router, router bits and a dovetail guide to slalom the cutter head through the tines. Were they to enter this in a furniture competition for handmade pieces where the entrants were required to hand cut the dovetails, well, that would be cheating. But even then I think that much of it depends then on the rules. I think in many cultures, leaders as politicians are expected to cheat. They’re voted in to their top jobs and people seem surprised when they cheat wherever they deem it fit. Whereas it shouldn’t fit anywhere, they capably seem very apt to manipulate, lie and scheme. In my world today it would be the audience that would shout cheat if they saw me pull out chopsaws, tablesaws and mortise machines even though I don’t disagree at all with them being used. Where it has gone wrong is that machines are so very exclusive and especially do they exclude young people and children in particular. I could go on but let’s leave it there.
Excellent article/blog post. Thanks for sharing!
My personal opinion (for what it is worth) is that the milling process (jointing, planing, getting to four-square) can be done by machines because this used to be done by apprentices in the day. Doing the remaining work (cutting joinery, etc.) by hand still qualifies as a hand built item in my book.
The big thing IMO is to not be too nuts about it. Everyone contributes to the craft in their own way, and helps to keep it alive.
Hi Paul, just looking at Hannah’s apprentice piece box, and she’s designed the front of her box/cabinet in the same way I did on a writing desk with the dovetails looking to the front of the piece. It’s an arts and crafts style thing which really appeals to me. As you mentioned in another blog recently it’s really not traditional to do this, and maybe stick to the traditional, but I think it looks really original. Did the same thing cross your mind when you saw Hannah’s box. By the way the box looks great, a credit to her skills.
I hope I didn’t give the impression that the overall box was her design. It’s not. It’s one of the pieces I designed to be made in my month-long furniture and cabinet-making course where we make a series of six projects including a Craftsman-style rocking chair, an oak coffee table and the tool chest replete with drawers. Her input extended beyond with one or two additional features.
Well it looks great. What a fantastic course that sounds, it must be a wealth of information and inspiration, especially for the younger generation of woodworkers .Many regards.
Just a quick thank you for suggesting vintage brass back saws.
I’ve bought a couple of R Groves saws, a 10″ and 14″. The 14″ is fine, but the saw blade in the 10″ was kinked and damaged. I put in another 15tpi 10″ blade from a modern maker because honestly the Groves Brass back feels like better quality and is nicer and it saws excellent!!
The modern blade is a bit thinner, but it works fine. Toothline is almost perfectly straight, tiny deviations, but saws perfectly straight and square.
Thanks for suggesting this somewhere. That vintage weighted brass back is really really nice, especially with modern steel.
Old brass with new plates, ah yes, lovely!
Hi Jasper,
I just saw your comment about the Groves saws and the ‘kink’ in one of them.
I had a similar problem with a backsaw some time ago, searched on line and found a Youtube video with excellent guidance on how to fix it. You will not be surprised to learn that the chap on the video is none other than Mr Sellers! (I have put the link at the end).
The method Mr Sellers demonstrates works well but I needed a few practice shots initially. The first problem was due to the fact that I was not doing it on a solid workbench surface – so quickly realised the importance of that. The second problem came from my innate caution and not wanting to ‘overcook’ it by hitting too hard. At least there is no harm in a little caution at the start! In the video, Mr Sellers also demonstrates what to do if the brass back needs straightening. I have not needed to try that and, from your comment, it looks as though you do not have that problem. The technique does, however seem pretty straightforward and worth bearing in mind.
I have a Groves saw which is a delight to use. Comments I have seen from other users (including Mr Sellers) all seem to rate them highly.
Link to Mr Sellers’ video on straightening backsaws: –
https://www.youtube.com/watch?v=tzc4tQ5CRxk
Link to Mr Sellers’ blog about Groves saws here: –
https://paulsellers.com/2012/06/r-groves-tenon-saw-makers-of-note/
Whatever you do, do not be tempted to ‘recycle’ your Groves plate into cabinet scrapers. The saws are too valuable for that!
Thanks Ken!
I’m aware of this,
I removed my brass back and looked at the saw plate itself and it was a little kinked without the brass back on it. However it’s very slightly, so I don’t know if it will actually have a negative impact.
I’m filing / sharpening the saw plate now and will re-install the brass back and handle afterwards and see if it saws and tracks straight and squarely.
I appreciate you commenting and steering my in the right direction!