Just a Dovetail Joint
If I can cut a gap-free six-dovetail corner to a drawer in 20 minutes it’s because I am not rushing it. It’s also because of the practised structure of my making, the sharpness of my tools that are sharpened before they become in any way consciously dull and because the tools I use are customised by me for me. The soles of my planes wear unevenly and I flatten them about every year or two. It takes less than five minutes by hand on a true and tested granite surfacing block and leaves me confident that if there is a levelling issue in planing then it is me and not the tool. The planes I rely on in the day-to-day are not premium versions as I would never buy another premium plane because the Stanley (or Record but not Record Irwin) bench plane versions do everything that a premium plane will do (and better) without all the extra baggage that comes with ever-engineering and too much unnecessary weight.
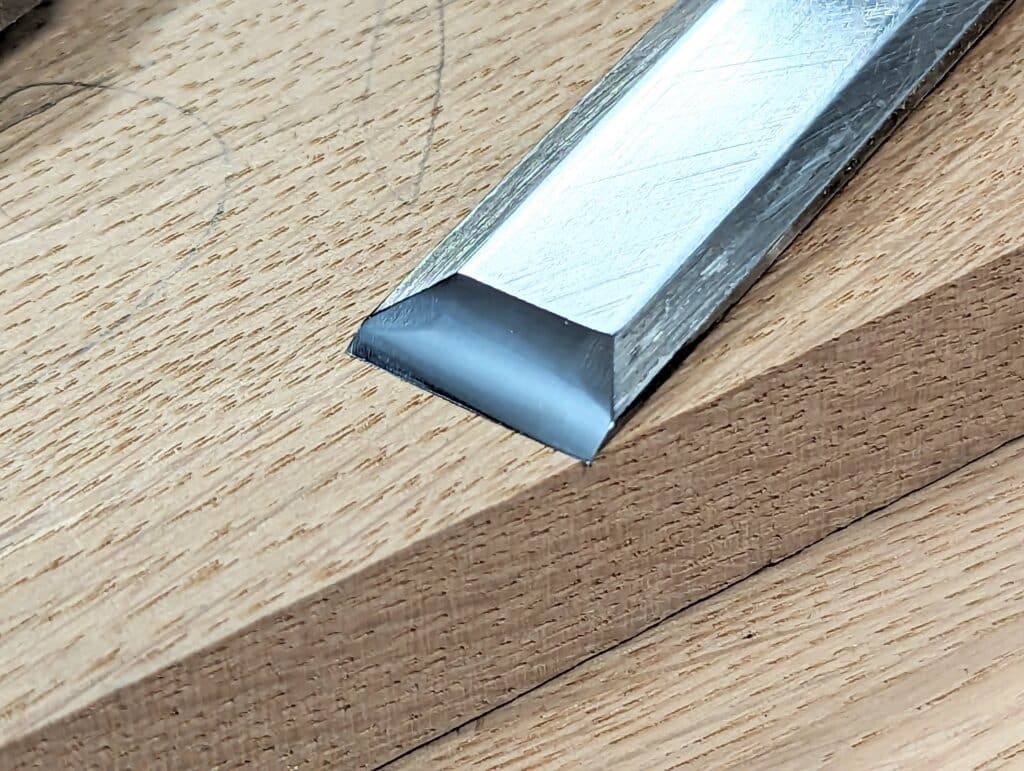
Someone commented recently on having to sharpen a plough plane iron and the inconvenience of it. I am never sure where this comes from. I must sharpen 20 of my edge tools two or three times every day. This is and always has been normal practice for me because I usually work a minimum of 8-10 hours a day working at the bench with my hand tools. I have gone through at least 6 #4 plane irons even though I do not generally grind my cutting irons on a machine grinder but use only abrasive grit of one kind or another. That’s roughly 10″ of steel and that’s only one of my half-dozen bench planes. So I have lived as a full-time maker now for 58 years and that’s 17,400 days so far and around, give or take, 139,000 hours of pure woodworking. So could that be 5.568,000 edges sharpened? It could indeed!!!
In making my dovetailed corners of my drawers I cut my sides and backs to fit dead tight to the openings with no margin. Why do I do that? Well, no matter how hard you try not to allow it, wood compresses with every mallet or hammer blow you make in driving a chisel into wood and then paring of the fuzzies on end grain reduces the length by a thou’. Now I know that some will disagree with me saying that but that’s of little consequence in the grand scheme of woodworking. Even with the knifewall wood still compresses and we woodworkers do our best to ensure it doesn’t but in my experience and the need to not live in an artificial world of the illusion of perfectness, walls get moved.
Making everything dead to the opening sizes, my drawers always seem to come out just right for the final planing to fit. This might be three to six shavings only. That’s close enough for me. The drawer slips into the opening quite nicely. Now I am just speaking the reality of what happens with wood overall and working with the more general hardwoods and softwoods at that. In rosewood or ebony, that will not be the case because of the density of the wood.
I prefer not to saw out the bulk of the waste with a coping saw because it seems to demand a compromise from me that I am unwilling to allow. It does not mean I never do it, and in this series of drawers I did use the coping saw for one corner, but that was just to offer an alternative to my audience. Generally, I see this as more a production method with a result that distracts me from a better method. You see it’s the fingertips close up to the cutting edge and the arrest I get up against the knifewall that matters the most to me and then the horizontal cut in towards it. Lifting out the waste and seeing the precision of the cut becomes the reflection of my efforts. Parallel this with feel of the cutting edge and its slicing cut on miniscule levels and suddenly woodworking becomes magnified to inexplicable realms.
Someone asked me why I polish out the whole of chisel bevels and it seemed more accusatory rather than enquiring. Well, it actually was a disapproval, I saw that. He’d bought into the micro-bevel, two-angle method but my macro-camber came from the ancients through centuries of well-proven technology which is quick to achieve freehand, non-invasive and more reliably achieved at that. As it is with using the coping saw to remove the bulk of the waste, I avoid unnecessary intrusions but that the addition of this third and fourth party interruption.
Back to the chisel. I can’t always explain the concentration of a whole body and mind to the chisel’s cutting edge and the placement of it in severing fibres. And I only explain it because, well, it’s an attempt to steer those woodworkers who might just miss quite a lot by using too much force to feel for what’s happening. The two or three fingers and the opposing thumb bring accuracy and concentration to the point of parting off in the movement developing the cut. We have the sense of feeling and seeing but then too there is the subtlety of slight sound. There is something that defies description unless you are a true wordsmith that also works and understands wood of any and all types. Of course, no one has such a thing, do they? That’s a luxury for anyone. This is a lifetime of learning and I am still on the journey knowing now that I can only truly know wood at a very finite level. I find scientists to be the most bemusing of people, especially those pursuing their microscopic invasion of the minutiae. It seems to me that they know the wood the least yet cannot seem to admit how little they really know. Imagine deciphering a drought half a millennia ago in a tree’s growth ring and never cutting wood with a sharp chisel or a good and well-tuned saw in the substance of making. I have been fairly disappointed with books from that side of learning but I am grateful for Bruce Hoadley’s endeavour to bridge the gap twixt the two realms. His book, Understanding Wood is a cover-to-cover read and I have read it three times over the years.
I might suggest relaxing in the making of dovetails. Compression in the wood is only intensified all the more when we ourselves are tense. Anxiety is the opposite of our goal to enjoy the process of woodworking. The fact that we have chosen high-demand processes that defy mass-making methods that are not really methods means we must dismantle how we were programmed to think and engage with our work. The immediacy of clicking, copying and pasting and hitting the delete button speedily through processes does not altogether work best for us. Better to leave that with the mass-makers for we are not nor ever will we be mere robots. You will be able to tell when you are too tense because the mallet’s drive will send the flat face of the chisel an extra degree into the knifewall and show as an unwanted gap. It’s always important to remember the rudder is the smallest part of the ship and yet it turns the whole ship as needed. Soo too those first strokes with the saw determine the direction of the saw in subsequent strokes. Taking time, allowing the saw to cut unforced, suggests great care to follow the lines placed to guide us. It’s all too easy in our excitement and uncertainty to drive the tools faster than they can accurately cut. we, you, have nothing to prove. Your choice of hand tools pushed the button to stop the conveyor belt so you could just get off.
Enjoy taking time. Examine your feelings to see what’s driving you. It doesn’t have to be slow, you’re just choosing something new to you; hand tool woodworking is a way of working that the ancients had and that was a measured control.
Hi Paul,
I noticed in the picture of the partially cut tail sockets that there was an apparent knife wall close to the end of the drawer front. I’ve not seen you demonstrate this method before. is this to protect the pin ends during construction, to be planed off during final fitting of the drawer?
Yes, sometimes there is a reason and sometimes none at all. But the knifewall cutline does stop fracture on the surface fibres after glue up where we subsequently plane the outside of the joints.
Thank you Paul. Today I visited the war grave of my great-grandfather in Wimereux, France, travelling from Australia. Paying respects to someone who had their time shortened certainly brings time into perspective. Listening for the chisel stop is indeed a gift.
I enjoyed this essay entirely. I’m going to be cutting my next dovetail in full mindfulness mode.
I thought the micro bevel thing was a lot of baloney… but it keeps being preached. It didn’t make sense to me but I’m from a different trade entirely and I wasn’t prepared to make a case against it.
I’m with you Anne. When I first started in the craft it seemed to be a superfluous step that further confounded the uninitiated. Being a newcomer I didn’t question or criticize. I got good results but the process seemed overly complicated. After applying what I learned from Paul’s videos my suspicions were proven.
I agree with David. I find that a micro bevel works as advertised. It works, but requires extra steps and doesn’t perform better for me than a smooth free-hand camber. I still sometimes add a micro bevel when I’m truing up chisels. I do this occasionally. I free hand sharpen for the most part, but now and then I’ll pull out one of the simple roller jigs and get a batch of chisels back to a specific known angel. After this, since I already have the jig out I’ll sometimes add a micro bevel. Doing this has been helpful to me since it provides a point of reference that lets me see where I’m landing free hand. Next time I sharpen the same chisels the micro bevel disappears into a smooth camber. I find I also get some interesting visual and touch queues doing this. I can feel where the two angles meet when I’m back to free hand. I also believe that the camber is preferable for some tasks like mortising where it seems to help the chips pop out. Likewise, I like the camber better for most tasks where I’m bevel down. Especially when free handing a curve for example. Folks should do what works for them, but for me I find free hand with a bit of a camber is simple, fast, reliable and works well for me.
I use the micro bevel, but not as it is “preached”. I still use my training wheels (Veritas honing jig), so a micro bevel is a good thing as it makes sharpening REALLY fast work since the bevel is tiny. Of course, once in a while I have to work on the primary bevel to grind it down – but I do that on very coarse sand paper (band sander band), followed by a quick tidy-up on the diamond plates.
For freehand sharpening, there is no need for it – or if you grind a hollow bevel.
Several ways to skin the cat, but the fastest method is of course freehand with a convex bevel.
I’ll probably get there some day, but for now – training wheels and a micro bevel. It gets the job done for me. “YMMV” 🙂
I think it is worth saying here that procrastinating over establishing the skill of freehand sharpening only postpones the establishment of a lifelong ability and self correcting as a self-discipline in any woodworking event is best established early on otherwise you will most likely never be free from the added steps in between the constancy of the supremely sharp edge.
A very sound advice, Paul! And I will follow it. I know where I have to go, but I struggle to find the time. As the kids grow older, I’ll get more “me” time. For the time being, though, the kids have priority.
Especially when Rosemine asks me if we “can build something with my tools”. She has a pink chest of tools, and I have a spokeshave with her name on it… 🙂 THAT is quality time!
But I get the advice. And I can see where developing this skill will aid me in other areas as well. Thanks for pointing me in that direction, Paul! 🙂
I think one thing that is well worth noting here, Anne is that apprenticeships generally disallow being sidetracked. There was good reason that crafting artisans did not use micro-bevels nor honing guides and even grinding wheels were a technology of the day but without electricity or even gearing but mostly treadles and handles turned by apprentices. Adding the electric motor simply replaced added labour. I actually use a hand-cranked grinder and a buffing wheel on it too. Although they are minimally used and mostly for simply grinding mild steel and such, they are there if I need them. They are no more or less handy than an electric version and there is nothing wrong with using electric equipment (in my view) just that for the main part they take up space and grind off more steel than necessary if used for grinding chisels and plane irons so I don’t really use them for this. So. as an apprentice and following thousands upon thousands before me, most craftsmen disallowed honing guides and even secondary bevels following using the grinding wheels. Within maybe two hours I had sharpening freehand down and that will be the same for anyone persevering to establish the skill rather than substituting for it. In the early days, someone might keep trying the freehand and even correct inaccuracies with a honing guide after persevering. I think that is a good strategy but, as I have said frequently enough over the past decades, use them purely as training wheels and not a replacement for skill. Oh, and there is no faster method for sharpening any edge than freehand, period.
Wonderfully written and thoughtful. Thank you. Now, if I could just cut a dovetail that wasn’t all gaps and fuzz myself…
Preach it, Fred!
I’m with you.
And I’m enjoying the journey.
“It’s always important to remember the rudder is the smallest part of the ship and yet it turns the whole ship as needed.”
“Enjoy taking time. Examine your feelings to see what’s driving you.”
“Your choice of hand tools pushed the button to stop the conveyor belt so you could just get off.”
The above quotes are indeed words by which to live. Especially for those of us who chose woodworking as a way to “get off of the conveyor belt,” as Paul says.
Paul, if you had chosen writing instead of woodworking as a career you would have been just as successful. This article proves that. If any of us are successful with our woodworking endeavors it is, in large measure, thanks to your ability to “work wood” and “wordsmith.”
“It’s always important to remember the rudder is the smallest part of the ship and yet it turns the whole ship as needed.”
“Enjoy taking time. Examine your feelings to see what’s driving you.”
“Your choice of hand tools pushed the button to stop the conveyor belt so you could just get off.”
The above quotes are indeed words by which to live. Especially for those of us who chose woodworking as a way to “get off of the conveyor belt,” as Paul says.
Paul, if you had chosen writing instead of woodworking as a career you would have been just as successful. This article proves that. If any of us are successful with our woodworking endeavors it is, in large measure, thanks to your ability to “work wood” and “wordsmith.”
well i m not a tatoo guy but this setence : . we, you, have nothing to prove. resonate enough in me for the idea to settle in my mind.
Thanks Paul for this humbling essay
Thanks Paul. The enjoy taking time comment you made resonates with me. It’s a hobby, I don’t sell my pieces – they are for the house or gifts to others. I have no reason to really care if something takes 30% longer. An example, I have made eight of the Paul Sellers clocks. I can get one done in 13 hours but I don’t enjoy it at that speed. If it takes closer to 18 hours, it’s a lot more fun. I’d rather it be more fun. It’s been about three years since I tried to see how “fast” I could get one done. I might do another one for speed just to see if my flow has improved – maybe I will make one out of walnut and butternut. Someone would like it as a gift or a donation for a charity auction.
The ahha! moment for me in this blog was the flat side of the chisel going into the knife wall. That explains alot to me. Thank you!
Beautiful reading, Paul! We all need to slow down and come back to a more sustainable living pace. I see we’re constantly losing the pleasure of taking our time to do things properly without forcing them. It’s almost like going hiking in a hurry, without taking the time to enjoy the landscape or smell the scent of the forest.
This little writing has given me an entirely different prospective on what I do as a woodworker…especially when considering dovetailing. Basic tools well-maintained. The feeling you are approaching the cut in a respectful manner. Relax. Thank you, Paul.
A little off topic, but we trust you for answers. Recently I misplaced my strop (since found) and required a keen edge. I found a planed piece of pine approximately 16”x4” and applied compound to the surface, after the required number of strokes, surprise, a nicely polished edge shone back at me. The results while paring was about the same as with the strop. Question; is this a viable alternative to a leather strop. Thank you for wisdom ,Don
I use both sides of my strop, the leather side and the wooden side. There is no doubt that the charge of compound on the leather stays in place and doesn’t snudge over into uneven globs as on wood so lether works best and the charge on leather lasts many times longer than on wood. I use the wood side very minimally and only really for flat faces.
Hi Paul, I’ve spent over 50 years working with wood, but one thing i’ve learnt is that we never stop learning, and I always enjoy watching your projects and the methods you use. I have to confess that these days I tend to use modern tools for a lot of jobs that I would have previously done by hand. However, I strongly believe its okay to mix both methods to achieve the best results.
I Notice that you use through dovetails for your drawer fronts, please dont take this as a criticism
its just an observation, traditionally we would have used a lapped dovetail in that situation, or is this a fashion of today, to show the workings to full effect. personally I like it very much, however i’m sure the likes of Thomas Chippendale would be turning in his grave.
Well, Alan, a couple of things really: Machines are machines and mostly they substitute for hand tools for different reasons some good and some not. Energy levels and time vary from person to person so that validates them. My audience wants me for the reasons I give which is that we can do a lot more with hand tools than we actually think we can when we master skills to use them. That said, if we start with modern machines (I assume when you say modern tools you mean machines whether hand held or freestanding) we rarely if ever become even remotely competent and confident with hand tools.
Actually, usually I would never use common or through dovetails on drawers and I haven’t actually done that here. These drawers are as yet unfinished.
And finally, you say you “have spent over 50 years working with wood” which of course is not a quantifiable amount to us. I know many people who “have been working with wood for years” but just for an hour or two a month.
Tangentially reminds me of driving a car (my Italian grandmother used to call them “the machine”). If you start with a manual transmission, you can readily go to an automatic and back to a manual whenever you want or need. Starting with an automatic limits what you can do in the future.
So very well said!
The drawers will receive a front face of the same wood as the carcass.
It’s wonderful how responsive you are to legitimate questions. Some might not find the time to refine and clarify issues already covered. But not you; you’re always educating, always lending a helping hand to those who reach out to you. Your generosity and care are exemplary. Thanks for all you do.
Chest of drawers. Can’t wait for this series to come through. that’s exactly what I want to build.