Relaxing Gets You There . . .
. . . better, more comfortably and more steadily!
The beefy, muscled arms bulb up into massive balloons and the knuckles whiten the more stroke on stroke. The rest of the body as a whole locks on and tightens up, tuning in to the intent of a forced compliance to power through with the strokes dead to the line yet with all of that intent the course of the saw is set on the wrong trajectory. It will not, cannot change even though the saw plate buckles and ripples beneath its stiff and rigid back. This is from my experience teaching some woodworkers new to the craft and hand-tool woodworking. The saws usually continue a steady path off course. No matter the power in the arms and upper body, without sensitivity, truly accurate cuts will not happen
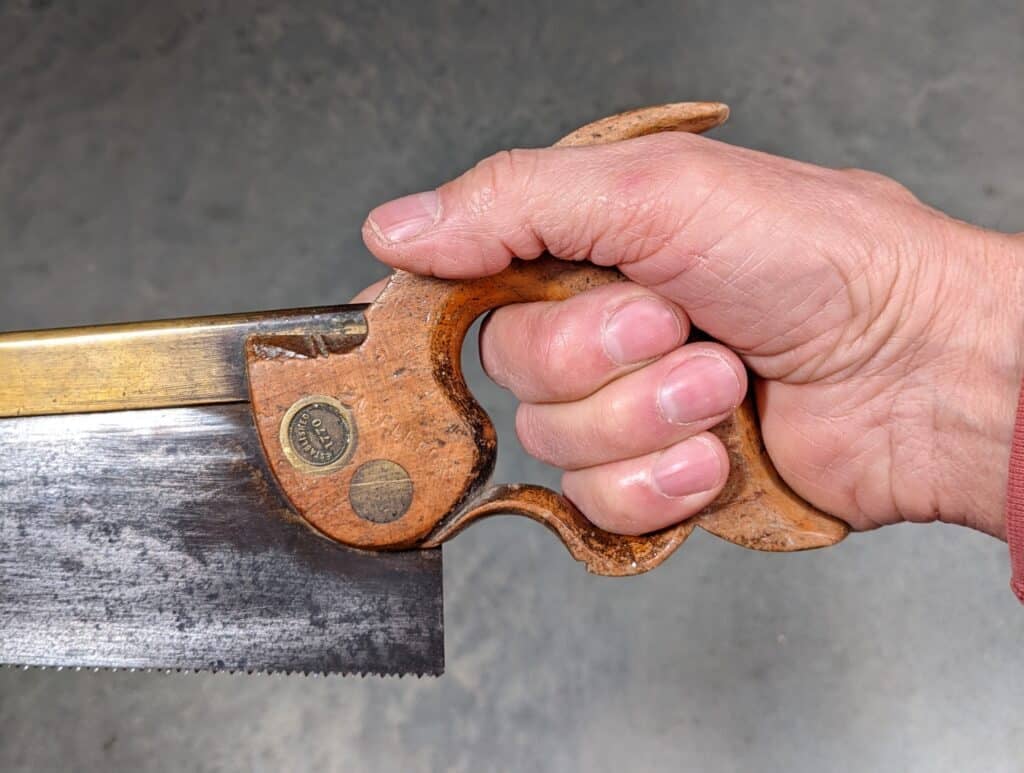
“It’s the weight of the saw and the hand only!” I say. “No rushing!” Since I began my apprenticeship back1965, nothing has changed and this is the wonderful thing about woodworking. In using most hand tools we need to master it’s less the hand tools and more our personal levels of sensitivity that need to change. What’s more, in 200 years nothing, nothing has really changed much at all; the hand tools are no different and certainly no better and the way they are to be used remains exactly the same. Of course, on some continents, the tools are pushed into the wood and on others they engage by pulling. Push or pull, both work equally well. No one way is better than the other. I see some of the finest woodworking ever produced on all continents in and from an era that knew no machines and both seemed to produce truly fine work.
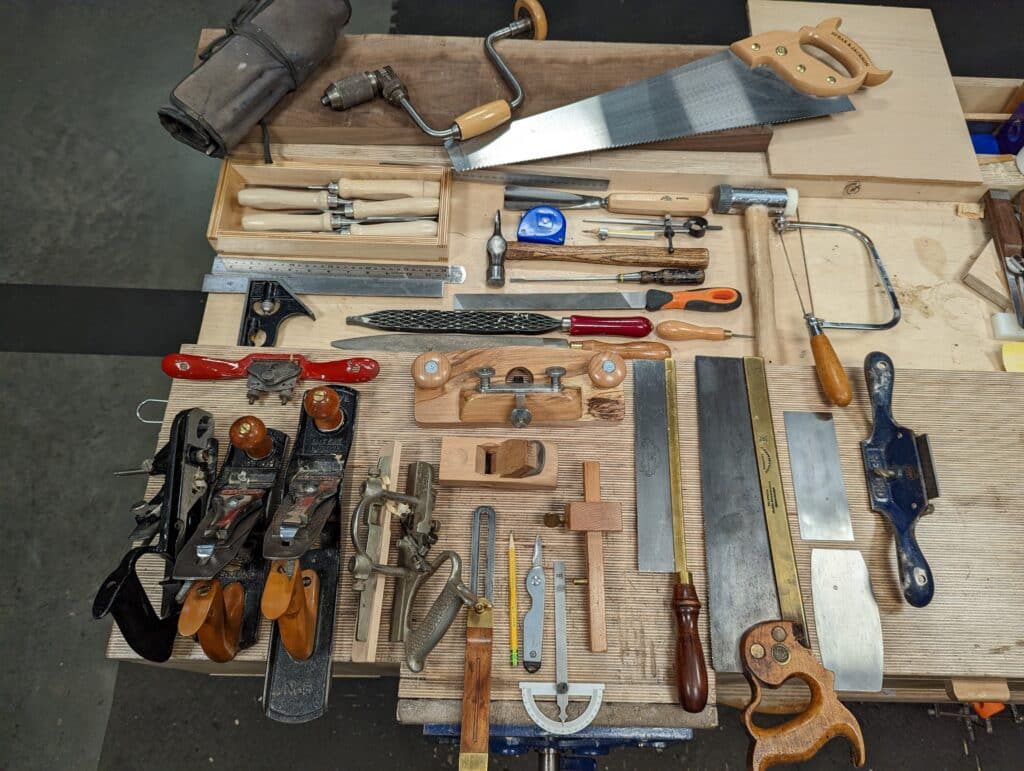
Unquestioningly, the basic hand tools we rely on, about ten only, haven’t changed much if at all and most of them obviate their purpose just in the looking at them. Beyond this early advice about not powering through by brute force, I demonstrated what I had generally taken for granted. When I started teaching and training with individuals as apprentices or students in a workshop setting for classes, one thing was certain. Most people saw woodworking with saws and planes as more of a forceful pursuit. Rarely did they put much if any faith in the saw or the plane but put their whole faith in the force of muscle and sinew. They were the power and they were going to power through with every cut until the fibres were parted off dead to the line. rarely if ever did this work. Mostly they seemed to dismiss any hand-to-eye coordination yet they did put unquestioning faith in the tool’s compliance according to their mental and physical demand. Then came my demo of linkage from the eye through the body to the saw tip; with the body totally aligned, feet positioned, saw hold firm and sight-line following through with each stroke, the easing of the saw into its passage gave effortless cuts of compliance. Finally, there is the pointing finger alongside the handle no matter the type of saw. This alone gives accuracy to the whole. Surprisingly, within minutes, they always seemed to get it. So it is with the precision a craftsman brings to the tools he or she uses. If that was how it was 30 years ago, how much more today when adults rarely receive any training in the use of hand tools from a practised user and especially a crafting artisan with decades of experience? Of course, we cannot dismiss the reality that most people engaging for the first time might use a low-grade or over-used tool and think force is the best or only course to make it cut. Without sharpness, hand tools don’t work. A blunt instrument destroys craftsmanship so it’s up to us to sharpen ten times more and ten times faster than we think we should.
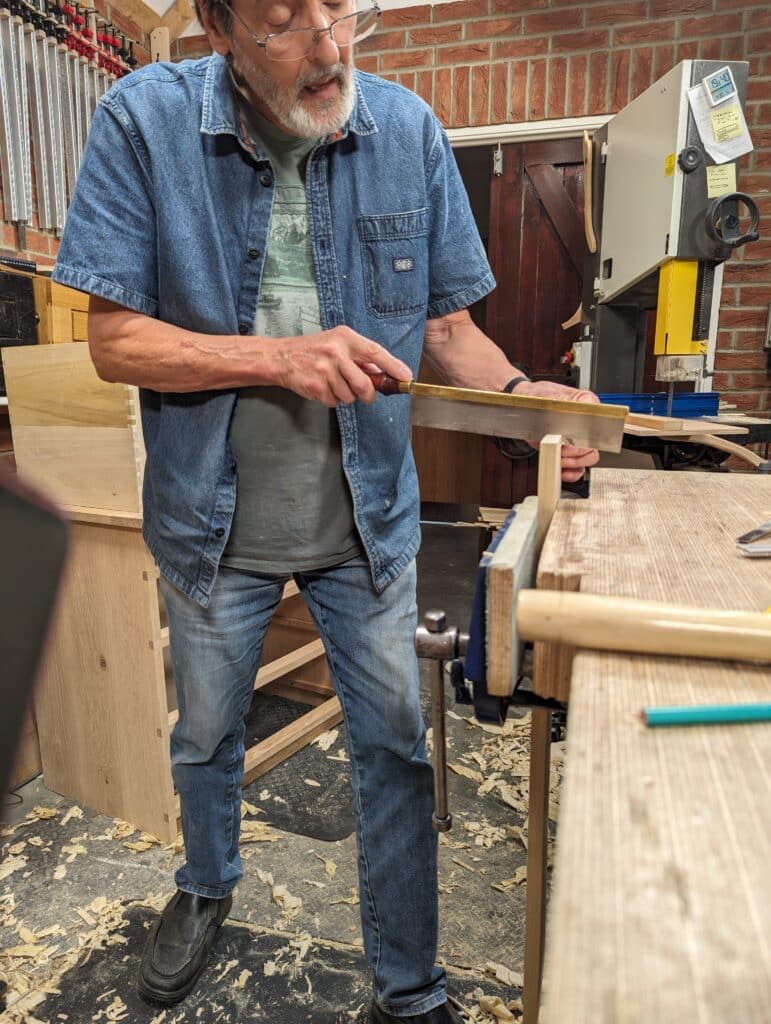
Now that that’s out of the way, my favourite small joinery saw, the one I rely on the most, is the one we call the gent’s saw. In my view, it surpasses any and all pistol-grip or closed-handle saws hands down and ten to one. These latter ones are good for 12″ and on up, but when it comes to a ten-inch long back saw it’s the gent’s that hits the mark every time. The key features are simple enough. I have seen makers change the shapes of saw handles to the detriment of the saw to make it look, well, maybe more Japanese-style. It didn’t work well at all and that’s because the British Gent’s saw in its origin was designed for push-stroke and not pull-stroke, two different animals altogether. One such maker took out the inline handle and sold only pistol grip versions which never had the same dynamic of an inline push stroke gent’s saw. This is where the engineer designer who does not use the tools starts to choose what he or she thinks to be best rather than listening to the customer or users in the know. But that’s water under the bridge. Let’s look at the best of gent’s saw features.
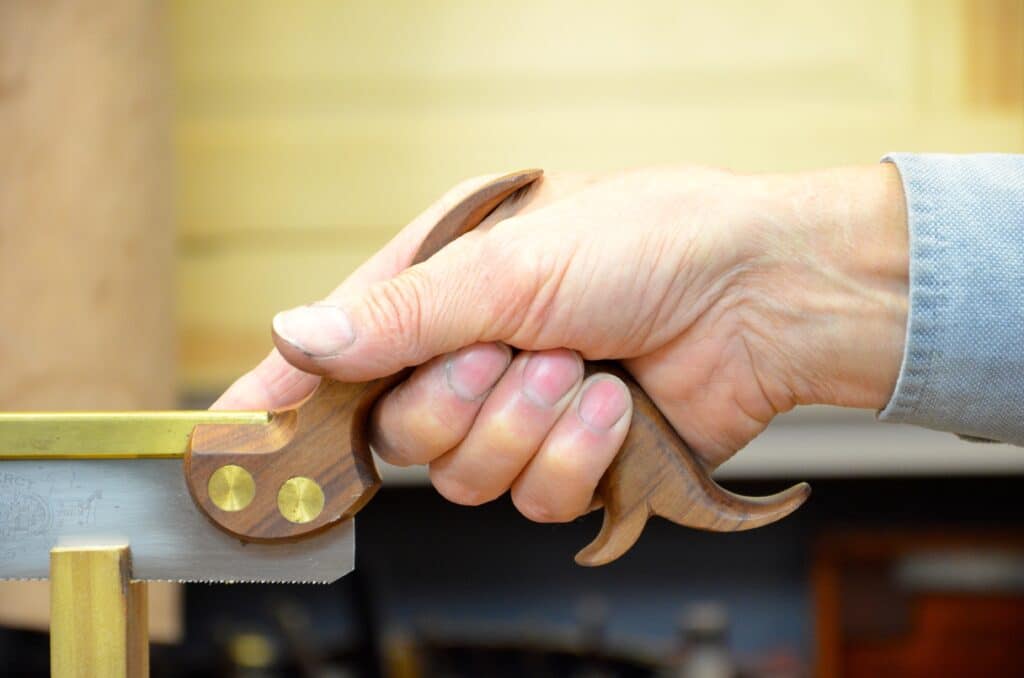
Longer handles might work well on Asian pull-stroke saws but on the gent’s push stroke, they hardly work well at all. Because Western push-stroke saws were under attack from proponents of Japanese tool sellers, manufacturers and magazine articles who in the 1980s and 90s extolled the virtues of pull-strokes for their thin kerfs and ease of use, Western saws with inline handles suffered a great demise. That for me was a truly sad conflict because such Western saws were remarkable tools in the right hands. The problem I saw was that, often, woodworkers had rarely mastered Western saws and Western saw sharpening too. Had they persevered they would have understood the dynamics of Western saws and enjoyed them as much as I do.
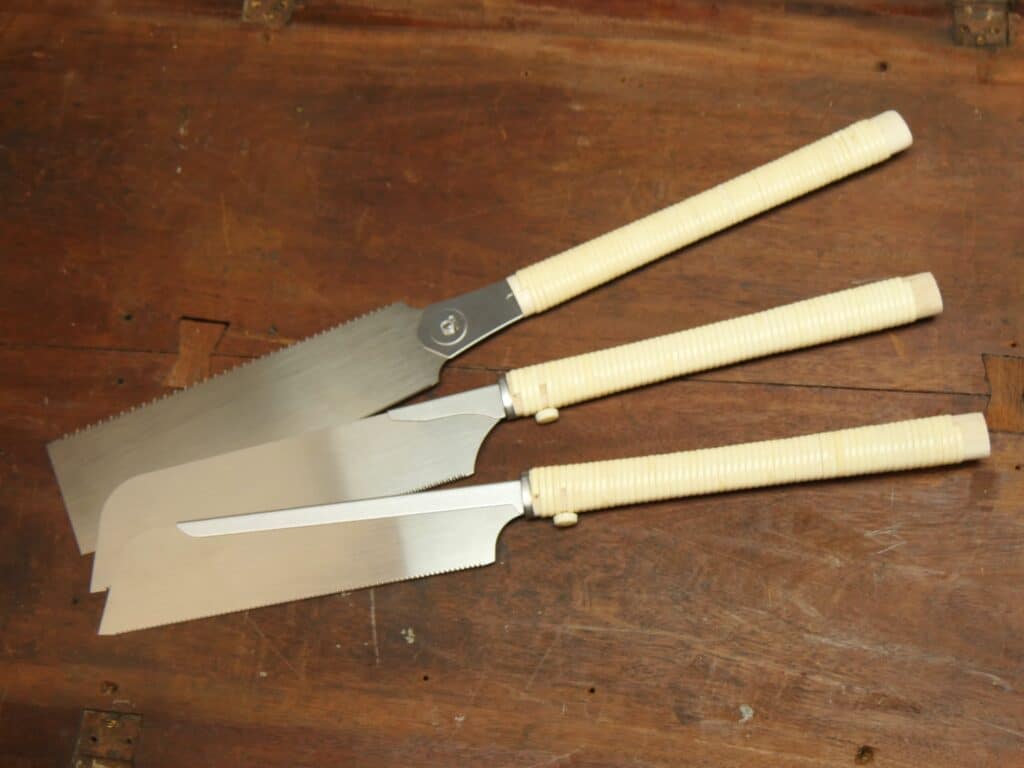
Straight-sided handles, tapered or parallel, don’t work very well on inline push-stroke saws. The shaped and bulbous handles solve all issues of functionality perfectly and indeed were ergonomically designed through the evolution of this 18th-century saw version because, in the end, all saws necessitate both pull and push strokes to return the saw to its initial cutting stroke with each push or pull.
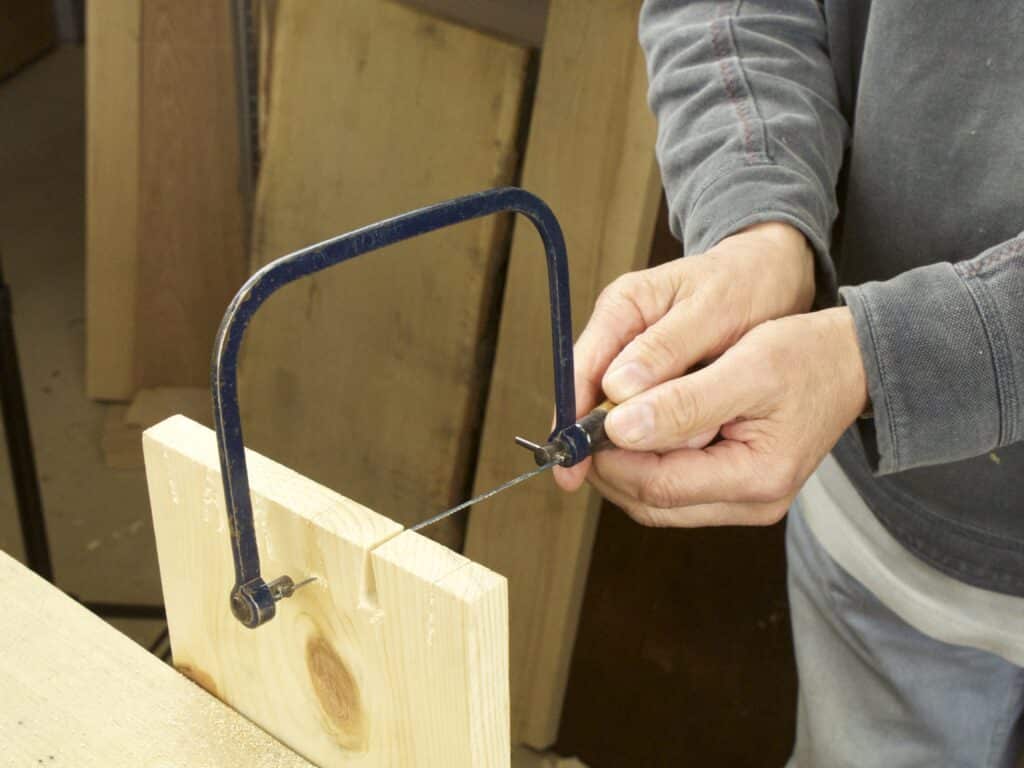
This handle is perfect. It fits into the palm hollow, the fingers wrap around the neck comfortably and the heel of the hand pushes the saw with the most direct, inline power possible and the fingers-wrap returns the saw to the start point for subsequent cut strokes. Of course, the amazing thing about the human hand in its multidimensionality is its ability to grip and fit just about any size and diameter of handle. The standard size of this traditional style handle is always well-suited to everyone be they large or small-handed. It’s easy to align the saw’s verticality to the cut or indeed adjust it to an angled cut instantly. The other types of handled saws often present problems to the user with oversized or too-fat handles, the wrong angle of the handle to the saw and so on. I recall one US maker supplying a saw he described as having the “perfect hang” when in reality it turned out to be the exact opposite and the saw was near unusable along with the handle being far too skinny.
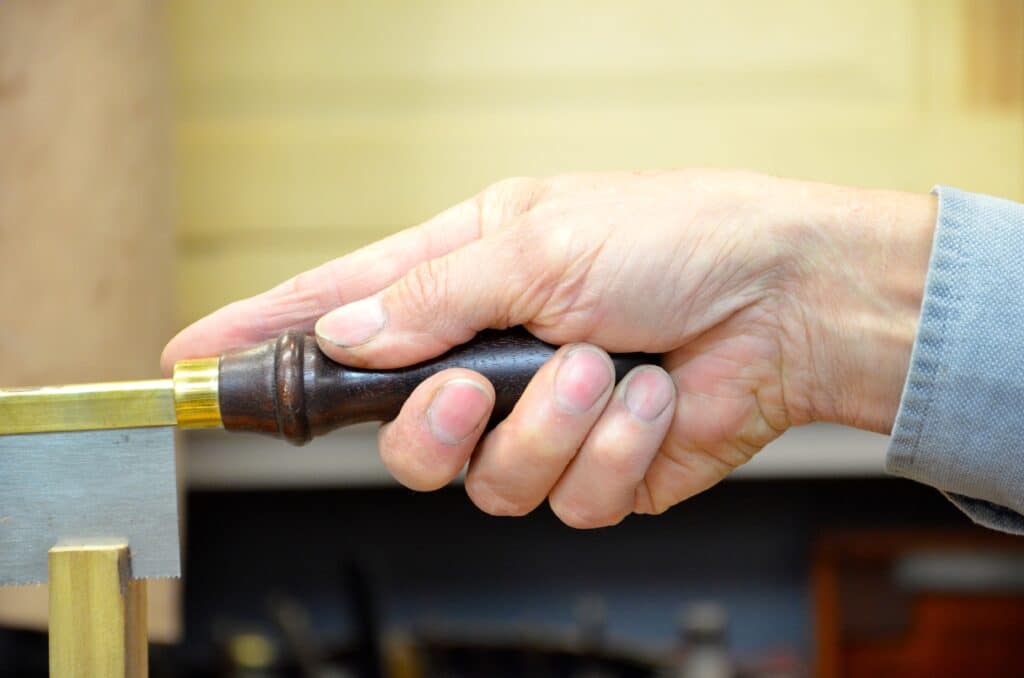
With any and all general sawing using a saw with a wide plate (in other words, not a coping or frame saw for instance) it is the opening six strokes that determine the direction of the saw. You cannot force a saw to change direction if, if, the saw is set correctly. Keeping the saw set to a minimum is always best with any saw unless you are cutting wet and saturated wood. We most of us rarely do that. Correcting your strokes early on is imperative. Once the course is set the rest becomes easy and the saw mostly follows the plate with only minor adjustments from us.
Conclusion: Chilling more, but still with determination, gets you there.
This is a nuance that changed my sawing forever. When I first started with hand saws, I don’t know why, but I thought I needed to put 2-3 horsepower behind my strokes. You know, like a table saw. And boy were the results awful. Even had the saw jump out my kerf once and chewed up the side of my thumb.
Today I was doing some remodeling and had to form fit small pieces to support new paneling. I decided to use my gents saw with a bench hook instead of a jig saw. It had been awhile since I used the hand saw and it was just wonderful! I will use my hand saws more instead of the power saws.
Love the picture of the basic tool group, really sums it up well.
Paul, your words ring true on so many levels. As I sit watching the sun crest the hill in the distance a hot cup of coffee and my well worn Bible on the table before me; I stop and give thanks for the moment. Oh, my mind could so easily go to all the very important things (to me) that must be completed immediately.
I think I will simply sit a spell with my Maker and offer a prayer of thanks for your polite reminder.
Your comments here are magnificent and ring so true with me. The Lord and Great Maker of all has given us these jewels of grain inside such beautiful wood, much as a diamond miner finds jewels buried in the earth. This “unearthing” we as woodworkers enjoy is yet another gift from God.
Thank you SO MUCH, Paul, for exposing us all to this magnificent thing called woodcraft. Blessings on you, your family, and your great team!
Paul you are right forcing the saw doesn’t speed things up. It just causes the saw to run off centre. However, when I was taught, the old coach builders who taught me said “when sawing look down your nose through the centre of the saw blade” and this has always worked for me to keep he saw straight. Bruce
Interesting tactic! I struggle with this, as I am left handed but right eye dominant. Thus when looking straight down anything, I’m never actually straight. When I play pool or snooker, it’s noticeable that I never look down the shot, but into it, and sawing is the same. Pretty much all my sawing is just left to trust in my body and senses to just be straight, and it seems to work! When I went clay pigeon shooting, it was suggested that I wear an eye patch (or just close an eye, which I did) and it was reasonably succesful. I’m reluctant to do the same with sawing, I’d rather work it out through sense and feel and hope for the best.
I have a friend who, about 60 years ago, started an engineering apprenticeship. Many of the tools were for right-handers only. Southpaws were given little thought or consideration. Tech drawing was challenging; metalwork lathes are tricky to set up for lefties.
Things are better for left-handed woodworkers. Planes, saws and chisels should not pose a problem and wood turning lathes can usually be set up for a left-hander easily enough.
I do not know much about the eyes except that having a strong eye and a weak one is not unusual and applies to me. Not sure if it is a problem for me when woodworking but may give an eye patch a test drive sometime. If it solves a problem I never realised I had, great! If not, I can practice pirate impersonations while sawing! To be serious, I think you may be on to something with the patch. Competitive archers, pistol and rifle shooters all seem to block the sight of one eye in competitions and my guess is that it is serving the same function as when you do your clay pigeon shooting or need a precise saw cut. The stance is also important in shooting. Partly for comfort but also for consistency- again, those are vital aspects in woodwork.
I love the photo of the tools ! It sure helps to have a shorthand when cruising the boot sales (or vide greniers here). Could we get a secondary photo that shows all the items to sharpen the tools in the first set? As ever thanks so much for everything Mr. Sellers.
Ms. Sellers in the picture of the tools what is in the tool roll in the top left hand corner by the brace?
Mr. Sellers in the picture of the tools what is in the tool roll in the top left hand corner by the brace?
Auger bits most likely ☺
Auger bits going from 3/16″ up tp 1 1/4″ in 1/16″ increments.
After switching to this exact and inexpensive gent’s saw that Paul uses in his videos and resharpening it as he has shown in his video, it cuts more easily, tracks straighter and more precisely than any other of the far more expensive dovetail saws that I own. It is my preferred saw for dovetails as well as small crosscuts and tenons. The other saws sit idly in the drawer as this little 10” gent’s saw is just a dream to use. But new out of the box, one must easily sharpen it just a bit as Paul has shown, as its factory teeth are just not as sharp as they need to be to function as seen in his videos. The biggest sharpening challenge is the saw’s small teeth @ 17tpi and holding your file angle consistently. Using magnifier eye glasses will assist you greatly in doing this. It is as easy to do as Paul says using a light hand and consistent and numbered file strokes.
I am 80 years old and can do it easily and so can you.
So pleased you posted the hand tools you use photo. I am in the process of building up my tools for my new woodworking hobby, Paul Sellers style, and this is going to be invaluable, to make sure I get mostly what I need for hand tool woodworking. I can’t do power tools as my neighbours would freak with all the noise, but it doesn’t mean I cant do some beautiful projects. That’s what I love about your channel.
Thank you.
Thanks Paul. I can vividly recall the first few times I tried sawing to a line it was really difficult. I stuck with it and followed your teachings. The specifics durations below are a bit fuzzy but, I seem to recall after about 100 hours at the bench, I could pretty much saw to the line. By 200 hours of bench time, I knew I could do it. Just the other day, I had to cut something long and wide and it resulted in an awkward body position (for the feet and my back/body twist) to do it. I stayed relaxed, really made sure elbow, hand and saw were aligned and did the cut. I put it up to my square and it looked square off the saw. I quietly smiled to myself. It’s the little things in life.
The moment I realized that white-knucklin’ the saw did not help me at all, I started sawing to my lines. I loosened my grip, to the point where I almost drop the saw. The first 2-3 strokes I try to almost lift the tip of my saw – light, careful. Sawing air. Then the cut is started, I can let the weight of the saw do the job while I drop, drop, drop the heel.
Well, at least this is how it works for me. 🙂 And I can cut square and true, following my lines – most of the times.
Loosing the death grip really improved my work. Same thing with my planes. A light touch, and I do not get tired so soon.
I don’t like using the coping saw either. I chop the waste. I am going to use the chisel anyway, and chopping the waste does not really take longer – I save the time I would have to spend securing the work piece in different positions. Plus – I find the coping saw a bit awkward, really. I don’t feel that I am in control. Lack of experience, I am sure.